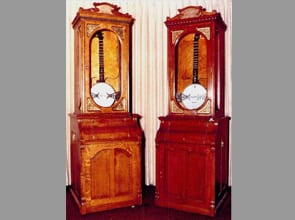
For complete Encore Banjo rollography click: https://www.rickcrandall.net/the-complete-catalog/
Rick Crandall (updated April 8, 2014)
The Encore Automatic Banjo has been in the spotlight as a prime automatic music collector’s piece ever since some properly restored machines were heard playing such old favorites as “Yankee Doodle Dandy,” “My Old Kentucky Home,” and “Maple Leaf Rag.” For those with a historical bent, the Encore lives up to its self-proclaimed title, “The King of Slot Machines.” Dating back to 1897, it was one of the very first commercially successful American coin-operated automatic music machines.
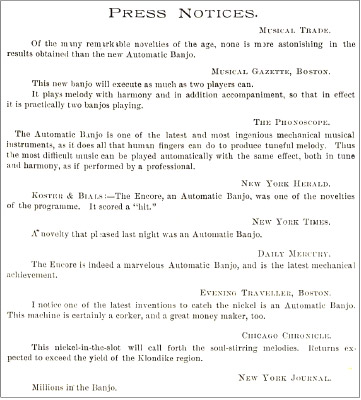
Figure 1a: Press clippings from 1902 – 03
Figure 1b: An original Encore (from the Bob Gilson Collection) beside a Dave Ramey Jr. replica. Can you tell? The replica is on the left.
The Encore is also the first machine of its type in modern times to be in such demand as to warrant the expense of being replicated. Today, over 50 excellent replicas, created by the D.C. Ramey Piano Co., are in collections, adding to the approximately 25 known originals. For more on replicas and restorations see: www.dcramey.com
Dave Bowers, in his Encyclopedia of Automatic Musical Instruments, gives the Encore top billing, with 21 pages of coverage and with editorial comments such as:
“The Encore Automatic Banjo is today one of the most interesting automatic musical instruments which have survived from years ago. The concept of a real banjo automatically operated by tiny mechanical “fingers” and playing in a very realistic manner is a fascinating one.”
The banjo itself was designed for the machine rather than for manual play. Its squared-off neck and wide string spacing make it difficult to play by hand. Even so, I had the good fortune of discovering a worn carrying case with an original banjo from an Encore inside. Someone had removed this banjo from an Encore machine, drilled in a fifth peg for the short string, and obviously must have played the instrument manually.
Also Included in Bowers’ Encyclopedia was a listing of over 100 of the 900 letters and corporate records from the original files of Mr. C. B. Kendall, the entrepreneurial spirit behind the various Banjo companies.
Dave Bowers sensed my own passion for early instruments and their history and thoughtfully parted with his Encore files. These have served as a base to which other literature has been added, including the library of the defunct Boyer Museum of Coin-Operated Machines of Chicago. See: https://www.rickcrandall.net/boyer-coin-op-museum-2/
Figure 2. Introductory page to an original Auto Manufacturing Co. President’s letter book.
The collection of records from the critical 1900 to 1904 period of the various banjo companies is one of the most extensive document libraries preserved associated with an early automatic music machine. Also included are records of addresses of Encore’s on location, music roll lists, corporate contracts, and of course, Kendall’s letter books produced and kept by his secretary.
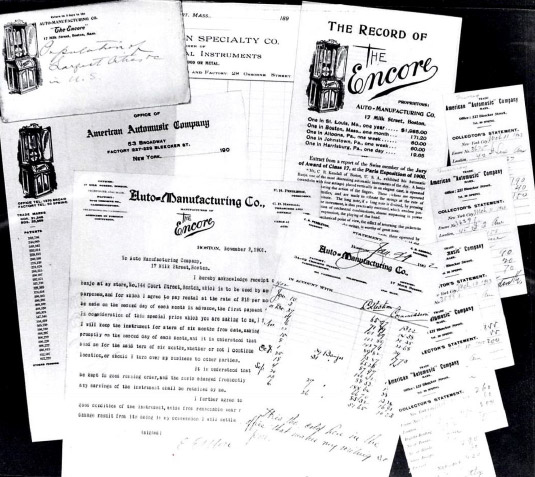
Figure 3. Assorted paperwork from both the New Jersey and Boston companies.
In-depth studies of early machines, such as the Encore, the Wurlitzer Harp, Peerless nickelodeons, the Gables Automatic Entertainer, etc., would reveal a fascinating fabric of technical innovation, entrepreneurial hardships, and marketing aggressiveness. In the case of the Encore, we have a wealth of information to draw upon.
Who Invented the Encore Banjo?
One of the many fascinations that turn-of-the-century mechanical music machines hold is the tangible evidence of the unstoppable inventiveness of the day, despite limited resource availability. Often it was one person who masterminded a new breakthrough – such as J. W. Whitlock with the Wurlitzer Harp (1899), John Gabel with his Gabel’s Automatic Entertainer (1905), and Henry Sandell with the Mills Violano-Virtuoso (1906). So why has obscurity enshrouded the inventors of the Encore Banjo? After all, it does hold an important position among the earliest of the music machines.
The search begins with the patent listings on the crest of the Manhattan-type Encore, shown in Figure 4.
The early patents listed date back to June 14, 1881, but have nothing to do with the Banjo. The first 17 patents originally belonged to John McTammany, Jr. of Cambridge, Massachusetts, the self-proclaimed (proven only to some) inventor of the perforated roll-operated musical instrument. McTammany showered the patent office with applications and was granted hundreds of them. His proximity to Boston must have brought him in contact with C. B. Kendall, the prime mover behind the commercialization of the Encore.
Figure 4. Top: Boston crest. Bottom: New York crest with patents
The seventeen McTammany patents purchased by Kendall covered the various aspects of perforated paper-roll operation, roll frame and tracking bars, treadle operation, endless-roll as well as rewind-type roll operation, and the combination of a bellows (“pump”) and actuators (“pneumatics”) for reed lifters.
The last of the purchased McTammany patents (U.S. No. 400,102) was granted on March 26, 1889, and there is indication that the first Banjo people were in some form of operation just a year later in 1890. Here is a quote from a later Encore advertising piece:
“The patents owned and controlled by the American Automusic Co. of N.J. [a post-1900 Automatic Banjo company] cover in its entirety a new and important branch of Musical Art, viz. The Automatic Operation of Picked Stringed Instruments such as the Banjo, Guitar, Mandolin, Zither and Harp and the various combination of these which will be effected through the natural development and evolution of this novel application of mechanics.”
“The experimental work in this field, which was successfully terminated by the close of the year 1897, covered a period of about seven years and represents the labor of some half-dozen different inventors and mechanical musical experts whose interests have all been acquired by the American Automusic Co. by purchase and assignment.”
“It may be added that this list [of patents] embraces absolutely all the Letters Patent of the U.S. in existence which relate either specifically or remotely to the art under discussion and therefore that the protection afforded to the enterprise is as full and complete as is possible to attain under this form of special privilege.”
The Encore entrepreneurs thought they had a monopoly on mechanical picking of all kinds of stringed instruments, but the monopoly was not as tight as Kendall thought, since J. B. Whitlock of Rising Sun, Indiana, was granted a patent in 1899 for a mechanically picked harp, which was also judged in its patents to be usable for “banjos, guitars and mandolins.” It is true that Whitlock’s picking method is entirely different from that of the Encore and more suitable for a harp, since a softer pick is achieved.
The Banjophone
In the January 13, 1900 issue of the Music Trades Review, another automatic banjo device is described in a manner that makes it sound as though commercial availability was imminent, although none are known today. The Banjophone, like the first incarnation of the Encore, was based on electromagnet actuators rather than pneumatic. Here are excerpts from the article:
Figure 5: Banjophone depiction in the Music Trades Review Sept. 2, 1899.
“Among recent applications of electricity in the playing of musical instruments, is the system of the Pianophone Company, 46 East Houston street, New York, which shows much ingenuity in its development and in operation gives very satisfactory results, says the Electrical World and Engineer. The company is producing self-playing banjos and self-playing attachments for pianos, the electric current doing all the work, no wind instruments or apparatus whatever being employed. The construction and operation of the self-playing attachment for the piano and of the “Banjophone” will be understood from the following description:
An electric motor is placed inside of the piano case at the base, and is belted to the mechanism which unrolls the perforated music roll and to a long steel roller. Over this roller, which forms the common return for all the key circuits, is a row of small horseshoe electromagnets set vertically in a frame, with their poles upwards. Immediately above the roller is a frame carrying a set of small contact brushes of wire, of which there are as many as there are magnets.
The perforated music paper passes over the roller and under the contact fingers, and as the perforations pass under the fingers the latter come into metallic contact with the roller underneath, thus closing the circuit through the corresponding magnet.
Behind the neck of the banjo, which stands upright in a cabinet, are four parallel vertical rows of solenoids, eleven in each row, or forty-four in all, there being forty-four notes on the banjo. To the core of each solenoid is attached a wire rod which passes through the neck, the end of the rod being flattened and bent at right angles over but normally clear of the string underneath. These finger pieces “fret” the instrument. When a current passes through a solenoid the core is drawn in and the finger presses down upon the string. When this occurs another action takes place simultaneously, i.e., the picking of the string and the sounding of the note.
At the lower end of the rod is a projecting finger which “picks” the string. All four rods are alike, and it is evident that the operation of the solenoids frets the string and strikes or picks it at the same time. These devices are the invention of Mr. G. Howlett Davis, who is president and general manager of the Pianophone Company.”
Jacquard Loom to Music Machine to Computer
History buffs will be interested in a comment in one of the McTammany patents from the Encore list that speaks of his invention in relation to automatic musical instruments “which are operated or governed by means of a perforated sheet of paper or other material constructed somewhat upon the principle of the pattern-cards of a Jacquard loom.” The Jacquard loom is an early 1800’s weaving machine controlled by punched cards much like the first computers of the 1950’s. It is amusing to think that the Encore may be the “missing link” between the first example of programmed automation and the most modem fields of electronic computing. It certainly is an established fact that there were ties of some kind between the Englehardt Piano Co., makers of the first coin-operated piano around 1898, and the American Automusic Company. The link further extended to Sperry Rand Company when it reputedly acquired Englehardt. Sperry was the developer of the Univac 1, the first commercial computer. This suggests a thread (albeit thin) from the Jacquard loom to the McTammany player reed-organ to the Encore Banjo to the Peerless nickelodeon to the Univac 1 computer … each a first in its class!
Back to the subject at hand. The first patent (U.S. No. 488,520) that actually dealt with a banjo was filed on March 9, 1892, and granted on December 20 of that same year. The inventor was Willard Gilman of Boston. The patent was for an electromagnetic device that could be used for a banjo, mandolin, harp, or other similar stringed instrument. Its conception was simple enough. The picking was done by a star-wheel positioned over each string that plucked the strings with no return motion – much like a musical box “plucks” its comb. The closing of an individual circuit would advance the appropriate star-wheel and play one note. This model used a five-string banjo (unlike the commercial Encore’s four strings), and all five pickers were controlled by roll perforations in the rightmost five consecutive tracker positions. Metal fingers felt for the holes in the roll in a fashion similar to that in the later Violano-Virtuoso.
On October 3, 1893, Gilman was granted patent (U.S. No. 505.878) for perforated sheet music. The five picker holes were moved to the left, and provision was made for coin start-and-stop operation. The patent claimed applicability to any fretted instrument, this time including violins and guitars, clearly a shotgun approach to broadening the patent, since no one would stand for listening to a picked violin for long!
On October 8, 1895, Gilman was granted a patent (U.S. No. 547,544) for a coin slot that differentiated between coins and avoided the insertion of undesirable foreign matter dropped into the coin chute. This latter feature is undoubtedly what avoided rejection by the patent office, since patents back to 1890 (U.S. No. 339,069) exist for coin-slot operation. Many other coin-slot patents were granted subsequent to Gilman’s, and no infringement cases are known.
On April 14, 1896, at the hands of the same attorneys that Gilman used, William S. Reed of Leominster, Massachusetts, was granted U.S. patent No. 558,419 for pneumatic picking and fretting on a five-string banjo. The application was filed three years earlier on June 23, 1893, so apparently there was some difficulty in approving the patent.
But Gilman was still at it, and here we get confirmation as to the existence of C. B. Kendall and the American Automatic Banjo Company, the earliest corporate entity involved with the Encore. Gilman filed a patent on July 21, 1894, for certain electromagnetic banjo improvements, and the application provides for assignment to the Banjo company. Not only was the company formed, but Kendall was involved, since he recalls in a later history (he wrote in 1904) that:
“The first automatic banjo was constructed upon the electro-magnetic system, but the magnets then used were of the telegraphic type, too jerky and noisy to be practicable. Furthermore, the only electric current available was taken from the street lighting lines at 110 volts, which caused so much sparking upon the perforated paper music as to sometimes burn them up and endanger the premises. At that time the then existing storage batteries were out of the question.”
W. H. GILMAN.
ELECTRICALLY OPERATED STRINGED MUSICAL INSTRUMENT.
No. 488,520. Patented Dec. 20, 1892.
Figure 6. First page of Gilman’s early patent using electromagnets
The next model was made upon the pneumatic system and was deemed satisfactory [based upon the Reed patent). A company was formed and the business commenced physically located in New York in 1897. A system of exclusive agencies was established in various pans of the United States.
There was a flurry of seven patents granted in 1898, two of which were attributed to Kendall. It was then that Walfrid Gustofson of New York City was granted patent U.S. No. 606,207 that included an improvement in the pneumatic picking device that most closely resembles the style of pickers on machines that survive today. Its innovation is a pin following an elliptical hole in a wafer that forces the picker to travel in an elliptical path across the string. The picker picks the string once and then returns to its original position without hitting the string on the backstroke, immediately ready to be activated again. The action is reliable and very fast. A good guess is that Gustofson was employed by the New York company and contributed to a divergence in design between the New York and Boston factories.
Many more patents were filed and granted, indicating a wide range of experiments. After Gilman had his original electromagnetic banjo conception completed in early 1892 along with Reed’s important pneumatic improvements completed in the middle of 1893, the rest of the patents were engineering improvements.
It therefore seems that technically Willard H. Gilman invented the original concept of an automatic banjo and
C. B. Kendall was the entrepreneur, technical contributor, and early financier who rounded up the necessary patent protection and pushed developments to the point of commercial release. The date of Kendall’s earliest involvement can be tracked back to 1894, but it is likely that he was the original prime force in 1890.
Figure 7. Gustafson’s picker patent of 1898 that made the
Encore functional in the sense of achieving “commercial grade.”
What were the Different Models of the Encore?
The answer to this question has taken quite a bit of unraveling, and there is more that can be done as data is collected on the remaining existing machines. There is strong evidence that the first automatic banjos were produced in 1897 before the Encore name was conceived, and they were of the Gilman electromagnetic type of technology. There are no known surviving examples. It is likely that however many were produced, they were scrapped and converted to the first Reed-type of pneumatic version. This version was sufficiently perfected to be sold commercially.
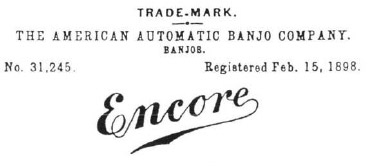
Figure 8. Encore trademark.
The Encore name was first used in May, 1897, and trademarked later in that year. It appeared both in the crest casting and inlaid with mother-of-pearl in the lower neck portion of the banjo. Later models used 3/32-inch German silver from which the Encore trademark was formed and applied to the banjo neck.
Figure 9: Encore banjo neck with inlaid mother-of-pearl floral pattern and applied German silver “Encore” logo.
Rick Crandall collection.
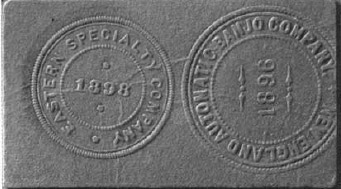
Figure 10. Corporate seals of the two New England companies.
The model differences can best be understood by clarifying the various corporate entities. In 1896 Kendall, in typical entrepreneurial style, complicated the corporate structure by establishing two principal companies, the New England Automatic Banjo Co. and the American Automatic Banjo Co. of New Jersey (but located in New York), each with its own factory. The New England company governed the rights to Massachusetts, Maine, New Hampshire, and Vermont, plus non-exclusive rights to foreign countries. Manufacturing rights for the New England entity were granted to a company already in existence and owned by Kendall, the Eastern Specialty Co.
Figure 11: Upper: Letter head of the Boston company; Lower: from the New York company.
The New Jersey company retained the rights to New York and the rest of the U.S. outside of New England. I don’t doubt that Kendall, a Bostonian, believed that was a 50/50 split: i.e. put New Jersey in one company and Boston in the other and the rest is whatever you can make of it.
In both the New Jersey and Boston companies, Kendall stayed somewhat in the background. W. Scott O’Connor of the later Connorized Music fame became president of the New Jersey company and came to own 3,869 out of the 3,889 shares of common stock. Mr. F. R. Pendleton became president of the Boston company on June 13, 1899. He only owned one share, and Kendall owned the rest.
Clearly, the American Automatic Banjo Company of New Jersey was intended to be the parent at least for a while, and all the patents were continually assigned to that company: however, a 1903 letter discloses where the real power lay, when Pendleton learned that Kendall had an option all along to buy the entire New Jersey company, including all Encores for $10,000 cash. Pendleton wrote of his 1903 conversation with Kendall: “He said he wanted to see the Auto-Manufacturing Company (Boston) get the Automusic Company (New Jersey) as was the original intention.”.
Kendall must have gotten this option in exchange for transferring the patents and prototypes to the New Jersey company. These two factories were the source of model divergence. The version of the Encore produced in Boston between 1897 and 1900 (of which 100 to 200 were made) was a somewhat more primitive machine. These machines can be detected by their early crest with the Encore name cast in script, rear-loading roll frame, and a valve chest that uses 5/16-inch diameter steel balls for valves. It was the valves that caused a lot of the trouble, particularly in picker responsiveness. As Kendall recalled,
“The pneumatic system did not continue as satisfactory as was expected, on account of the great power requirements to operate it, as well as its complications and the many troubles arising therefrom, and the limited area of territory that could be occupied, even in the large cities, because of the unavailable necessity of using the street-light electric current for a native power to operate the pneumatics.”
Both companies ran into severe financial trouble, and Kendall and O’Connor decided to re-form the companies and start over.
In New Jersey, the American Automusic Company was formed in April of 1899, still with W. Scott O’Connor at the helm. The Banjo business continued, but with a new style Encore that became unique to the New York factory. The valves already were completely different and more responsive, even though they were configured in an odd combination of a small pneumatic moving a lead valve. The roll frame was located in the front of the machine for greater ease of loading, and other improvements were made as to the durability of the machine. The cast-metal plate on the top crest had already been changed, giving prominence to the many patents that led to the current machine. The original company name, the American Automatic Banjo Co. of New Jersey, was left permanently cast into the plate of the New York machine and was never changed to the Automusic name. Somewhere along the line, the lower-front door-panel design changed from an arched inset to a rectangular pattern, but since the mechanisms slide in and out of the case easily (for repair), many times the door panels got damaged and replaced with newer doors. Earlier New York machines had a curved birds-eye maple shield around the banjo neck covering the fret pneumatics and later machines changed to a more easily produced flat shield that is the pattern followed by the Ramey replicas.
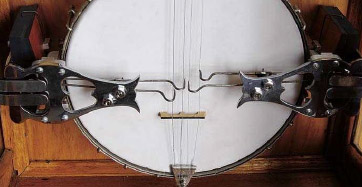
Figure 12: Boston version of the Encore. Left: note yet a third shape of the shield surrounding the banjo neck; Right: Picker mechanism unique to the Boston machine.
Figure 13: Rear-loading endless roll music arrangement on the Boston machine.
Figure 14a. Encore No. 1721 from the Figure 14b. A Ramey replica exactly duplicating
Hayes McClaren collection with the the later flat shield around the banjo neck.
earlier curved shield.
The New York machine was an improved device. The valves were improved by using a small pneumatic, which moved a flat lead valve. The roll frame was moved from the rear to the front of the machine for easier access to change the roll. Cosmetically, the cast metal plate on the top crest kept the original company name, the Automatic Banjo Company of New Jersey and listed many of the patents that led to the current machine. The American Automusic Company sold machines through several dozen sales agents, primarily music stores and arcade operators for prices in the $350 to 500 range. Machines were also put out on location under percentage leases where the location owner got 20% of the take. The play counter kept the count honest.
Figure 15. Basket holding an Encore endless roll. These were easily slid out to change rolls without rewinding.
Is this the first cassette?
The Boston companies took longer to re-incorporate, undoubtedly waiting for a successful response to financing proposals. Finally, the investment group of Davis & Soule of Waterville, Maine, put up the money, and the Auto-Manufacturing Co. opened its doors on March 2, 1901. The assets of both the Eastern Specialty Company and the New England Automatic Banjo Co. were transferred to the new operation, and its employment hit an all-time high of ten people plus Kendall. From then on, the Boston company went downhill, and the New York company prospered until 1903 or so.
Kendall was the driving force behind the Auto-Manufacturing Co. even though Pendleton was president. It is clear from the hundreds of letters that are in my files that Pendleton was incapable of handling the business, and Kendall’s participation, while erratic, was forceful and creative. During the year 1900, the music roll manufacturing part of the company split to form the Connorized Music Company with James O’Connor (presumably W. Scott’s son) as president and treasurer. James O’Connor was instrumental in the development of the first electromagnetic Automatic Banjo and he helped to perfect the later pneumatically-operated version.
The American Automusic Company, with W. Scott O’Connor remaining as president, continued to make the Encore while sharing the factory with the Connorized Music Company. The American Automusic Company provided a catalog of about 2,000 available musical numbers and tried to keep as current as possible to offer the very latest musical selections of the day.
The Boston machine was subject to some unsuccessful experimentation and change. For instance, instead of changing the valve arrangement, Pendleton searched for lighter aluminum balls to replace the steel ones. This quest began in March of 1901 and widened to any aluminum fabricator in the entire Eastern seaboard. None were found during years of searching. There is some indication of an order being placed for aluminum balls in 1905, but by then they could have only been intended for replacement parts since Boston Encore production had already slowed to a standstill.
The roll frame was kept in the rear, which caused some incompatibility and acrimony between the Boston company and the New York company. The latter company was the sole producer of the music rolls, which were set up in the reverse to what Boston needed. On the New York machine, the bass-string picker holes are on the left of the paper, and the paper travels downward in front. On the Boston machine, the bass picker hole is the rightmost position on the paper, and the paper travels up. The incompatibility was not great, since all that was needed was to turn the New York roll around, but there were problems nonetheless, since the lapping of the paper at the joints was wrong for the Boston machine.
Both companies used the same banjo parts (from the Boston company) and coin counters (from New York), and both switched from inlaying the Encore name in the banjo neck to surface-mounting a German-silver script Encore on the neck.
Figure 16. Unique among early coin-op machines was a four-digit pneumatically-operated coin counter used for checking cash box contents under percentage leases.
The Boston roll frame had paper-feed problems that were solved by replacing the wood rollers with steel rollers. The cast-brass decorative corners in the front door and sides were of either of two patterns: fancy curlicues or leaves. The castings were either unpolished brass or surface polished and nickel-plated.
Cosmetically, in both instances the case was made of solid quarter-sawn oak, but records indicate that a half dozen mahogany cases were made in both factories. These, along with some oak-cased machines, were used without a coin slot and coin counter as home models. The Boston company demonstrated the first home model in France at the Paris Exposition of 1900. Three of this type is known to survive.
Figure 17. Encore Home Model H2: mahogany case and no coin slot.
Coinage was both the nickel and the penny for the U.S. machines, but a few dozen went to England with either six-pence or penny slots. Strings came from the National Musical String Co., New Brunswick, New Jersey. An optional mute that pressed on and hangs from the bridge was offered, but no mutes have surfaced. A pneumatically-controlled mute that pressed on the bridge was produced on the later Banjorchestra machine that incorporated an Encore banjo
(see: https://www.rickcrandall.net/engelhardt-banjorchestra/)
The Motor Story
The motor was a story in itself. As far as Kendall was concerned, electricity, not women, was the source of all problems. The Encore was one of the first electrified machines, but that didn’t feel like an honor in 1898. You know the saying, “The earliest Christians get the best lions.”
Up to the mid-1880’s there was no central power generation. 1882 marked the beginning of Edison’s central power generation for incandescent lighting, begun in New York City. By 1891 the earliest patents for a DC motor were issued and the Crocker-Wheeler Electric Company (see end notes) had been formed (in 1890) with the stated goal “to make and market the first appliance motors.”
The first appliance markets for the “mains-powered” motor was for sewing machines and electric fans. However by 1898 another “appliance” had the need for a motor, the Encore banjo.
Figure 18: Crocker-Wheeler open-winding, 95 volt brushed DC motor used to power the early Encores.
Rick Crandall collection.
The prevailing electric current was non-uniform. DC current in New York was 95 volts and according to Company letters, other Encores had to run on 52 volts AC, 60 cycles, another at 104 volts, 40 cycles, and yet another at 62 volts, 135 cycles.
The New York Encores first operated with a version of the Crocker-Wheeler 95 volt DC motor that are a sight to see – and they still work today! This motor represents the earliest applications of mains power other than the arc or incandescent lamp. Later Encores used the Holtzer-Cabot motors (A.C. and D.C.) and then switched to General Electric. The Boston company experimented with storage batteries (they could run 10 hours, but were too expensive), spring-wound motors (not powerful enough), gas engines, and a foot-pumped banjo – anything to get away from municipal electricity.
Letters such as these were typical:
“Dear sir,
Your telegram just received as follows: `Five hundred volts direct current same as street car.’ We have been called upon before to run our Banjo on a 500 volt current and the only way that it could be done was by putting lamps in series as a resistance, but the fluctuation of the current was so great under these conditions that the results were not satisfactory.”
This one really takes the cake:
“Dear sir,
We have learned that there are two currents in Gloucester, a day and a night current, of which the day current is high frequency, and the night current is low frequency. The motor we sent you is the one adapted for the day current. We will express you another motor, low frequency, which can be used for the night current and you will be obliged to shift them every night and morning.”
Motors kept burning out. In a letter on October 21, 1902, from Pendleton to Holtzer-Cabot, the frustration is clear:
“Dear Sirs,
We are very disappointed that you did not ship the motor which we wished sent to Norridgeweek, Maine. You must have known that we were anxious for it, for we wrote a letter and then telephoned. The result is that one of our machines remained out of action for two weeks, losing us considerable money, and also hurting our reputation.
Why should one business house treat another as if it were a thief and a rascal, without any cause whatsoever?
Now the facts of the matter is just here: everything we send to you to be repaired we have to wait weeks and months for, and probably would never get it without constantly begging and pleading with you. And it is all because, presumably, you know that you are the only place we can go for motor repair work, consequently you can be just as disagreeable as you please.”
Figure 19. An original Holtzer-Cabot AC motor, rated at 104 volts.
The point behind this whole section on motors is that there were many motors that can be considered “original” for the Encore although the Crocker-Wheeler gets motor collectors’ blood raging!
Figure 20: Early Crocker-Wheeler motor powering an Encore Banjo. The endless-music roll in its basket is visible on the left and wooden coin box above.
How Many Encores Were Made?
There are many conflicting statements in the literature concerning the production quantities of the various models. The approach I took was to ignore all advertising claims and to rely upon the financial statements, production papers, and serial numbers of existing machines.
From 1897 until 1903, approximately 800 banjos of all models were made. This was an estimate made by Kendall in 1903 and handwritten in his own personal notes at a time when he was being negative about past accomplishments of both the New York and Boston ventures. Rather than being his normal puffery, this statement has some credibility.
Subsequent to 1903, there were few or none produced of the Boston machine. The Boston company had been stripped down to two employees in late 1900, and existing machines were circulated from one location to the next. New York serial numbers extant today range from 1721 through 4010. No. 1721 was from the earlier New Jersey company, and No. 4010 was one of the last to be produced.
Figure 21. Encore No. 2521.
Rick Crandall collection.
There may have been gaps in serial number ranges that mark the change-over from one company to another. At the present time, the best estimate of the number of original machines would have to be developed as follows:
Boston machines
Serials 50-100 – old style, 1897-1900
Serials 200-330 – later style, 1901-1903
Unknown Serials – approximately 10 home style
New York machines
Serials 1500-1800 – old style, 1897-1899
Serials 2000-4025 – new style, 1900-1908
Serials H1-H20 – home style 1900
Total Estimate: 2525 machines
If anything, this estimate is low. The Encore was therefore a success and sold in greater quantities than a number of other kinds of music machines. Among the novelty instruments, the Violano-Virtuoso is credited as having been a great success. It had the marketing prowess of the Mills Novelty Co. behind it, and during the years 1908-1928 a total of 4500 were sold – not even double the earlier Encore. There are approximately 25 original Encores in collections and undoubtedly at least several more yet to be found, which even if that adds to 30 is a low survival rate.
The novelty of an automatic banjo wore off as automatic coin-op pianos were introduced. The nickelodeon’s popularity soon made the Encore obsolete. In 1906, W. Scott O’Connor abandoned the automatic banjo business for the much more lucrative music roll business. The Connorized Music Company became a major manufacturer and distributor of player piano rolls and moved to a larger factory. James O’Connor didn’t give up entirely on the automatic banjo, however. In 1914 he introduced the Banjorchestra, an orchestrion that featured an automatic banjo identical to the Encore, but with drums, tambourine, castanets, triangle and piano added.
The Music
The original company records have two catalog listings that were clearly for internal use, perhaps for royalty payments. One is a ledger book listing 1565 tunes and the other is a typed list containing 823 tunes, some of which overlap the ledger. The combined total is 1800 unique tunes, although that is 500 more than is found on the 261 rolls that were produced, of 5 tunes each. Given that these rolls play only on an Encore banjo and are not ubiquitous as were the later A and G rolls that played on many machines, this is surely an enormous library. It further confirms the success of the Encore banjo.
Fig. 22a: Page from internal Company music catalog Fig. 22b: Five-tune card hangs on shield
The music plays the banjo in a range of styles from individual picking to rapid strumming mandolin style. The tune catalog has some of the earliest music styles including many tunes whose titles would violate just about anyone’s sense of “political” and racial correctness. The complete Encore Rollography can be found by linking to: https://www.rickcrandall.net/the-complete-catalog/. Some original rolls have been recut and others have been custom arranged by Art Reblitz who has done a masterful job of working the banjo to its fullest capabilities and has achieved very listenable musicality.
How to Find an Encore Today
The Encore is both highly desirable and rare, and, if properly restored, a fun-sounding instrument. This combination of factors makes it a very challenging acquisition for the present-day collector. Few original Encores come up for sale. The demand is high, and a market has developed for a replica that is now being produced in limited quantities by a topnotch restorer (see Figure 1b).
Those who seek the excitement of a “find” out in the countryside may wish to have the following information, although finding a machine previously undiscovered is pretty hard these days.
The last location of the factory of the Boston company was at 38 Osborne Street, Cambridge, Massachusetts. In 1906, there were upwards of 40 machines there. The New York factory was at 227-229 Bleeker Street, and upwards of 30 machines were there in 1906. Boston proper would not be fertile ground since the records indicate all machines in commission were removed from there on account of a switch to D.C. power in 1903.
The Maryland agent, F. W. Rohrs, Philadelphia Road and Hamilton Avenue, Baltimore, had a stock of about 15 machines that were found along with a dozen more in a pair of barns in the 1960’s. These were disbursed in groups, and not all the Banjos are in recorded collections. Fourteen of them were badly fire damaged, but parts from them were used as the basis for Ramey’s replica Encore.
Figure 23. This is the way to find them.
These are two New York Encores in the rough.
Single machines have been spotted or acquired from Northern Canada; Ithaca, New York; St. Louis, Missouri; Oakland, California; somewhere in Arizona; and somewhere in Texas. Seventeen machines were sent to the British Mutoscope and Biograph Co. in London in 1902. The author chased that lead to a theater at 18 Great Windmill Street and learned that the company moved to an address outside London before it went broke in 1907.
Originally, Encores were most popular in hotels, barber shops, lunch rooms, pool rooms, and drug stores. Relevant to all those, I would guess old storage rooms would be the best bet, since operators typically retired them from service as they went out of favor.
Geographically, I would concentrate in the action towns of the 1900-1908 period when most of the machines were distributed. Maine, Massachusetts, New York, New Jersey, Pennsylvania, and Texas should offer the best hunting. Of course, if you just have to have one and you’ve got some money to invest, your best bet is to make your desires known to the existing owners.
There are over 40 replicas around and they come up for sale fairly regularly. They look and sound great but from a value standpoint, know what you are buying, obviously a good original machine is rare and worth more and likely to appreciate more than a replica.
Credits:
Many thanks are owed to Q. David Bowers for discovering, preserving and offering the trove of original papers from the early Encore companies.
Also invaluable to this document has been the generous provision of many of the photos of actual machines by Encore restorer and expert Dave Ramey, Jr., whose company, the D.C. Ramey Piano Company (www.dcramey.com) has restored many of the original Encores and has produced over 50 replicas for the collector community.
Figure 24. Above: card that was hung on the shield surrounding the banjo neck;
Below: card that is inserted in the brass frame to the left of the coin slot.
End Notes #1: Encore Instructions
End Notes 2: The Crocker-Wheeler Story
All motors prior to the Crocker-Wheeler were battery powered curios for the laboratory and the classroom. This motor represents the first application of mains power to a device other than the arc or incandescent lamp.
Three personalities were behind the Crocker-Wheeler motor. Francis B. Crocker was an inventor and more. Charles G. Curtis was a partner. They took Schuyler S. Wheeler into their new partnership in 1886 called the C&C Electric Motor Company.
Wheeler, at 22, was one of the builders of Edison’s Pearl Street station and Crocker founded Columbia University’s dep’t of Electrical Engineering. Wheeler later founded what would become the IEEE.
Their goal: to make and market the first appliance motors.
From: The Electrical Engineer 1892, 27 Jul page 95:
The Crocker-Wheeler Electric Company, New York, have been in operation a little over two years. Last winter they paid a dividend of 5 percent, and they paid an extra dividend of 3 per cent out of the earnings of the company. Their business has increased so rapidly that they were compelled last year to increase their capital stock from $100,000 to $200,000. The officers of the company are: President, S. S. Wheeler; vice-president, F. B. Crocker; secretary and treasurer, D. H. Jeffery. The business this year has averaged several times as much as last year, and, notwithstanding their largely increased plant, they have been compelled to run nights to keep up with their orders.
Paraphrased by Time Magazine 30 Nov, 1942:
One model would be an electric fan, of which Wheeler may be said to have been the inventor, at least, of the first mains-powered electric fan. Another use of the motor was to drive the ubiquitous sewing machine. If as a tailor, you sew all day long every day an Electric Motor–fed for a penny’s worth, from Mr. Edison’s wire resulted in these little machines advancing tailors into the new age of labor-saving efficiencies. The power is taken off via a cleverly quick-detachable wooden pulley sized to accept round leather belting such as was used with treadle operated sewing machines. Imagine that one might obtain various diameters of pulley for particular sewing purposes or speeds.
It was the beginning of the electro-kinetic era.
Crocker and Wheeler differed in their aims from Curtis, and so the partnership with Curtis ended in 1889, Crocker and Wheeler went into successful collaboration, themselves as manufacturers of motors. In December of 1891 Crocker-Wheeler re-incorporated in New Jersey as the Crocker-Wheeler Electric Company, in preparation for relocating the company’s operations to Ampere, NJ.
In 1893 the company indeed moved their manufacturing plant to Ampere.
In 1942, Charles E. Moore’s Joshua Hendy Machine Works bought Crocker-Wheeler for $3.2 million dollars.